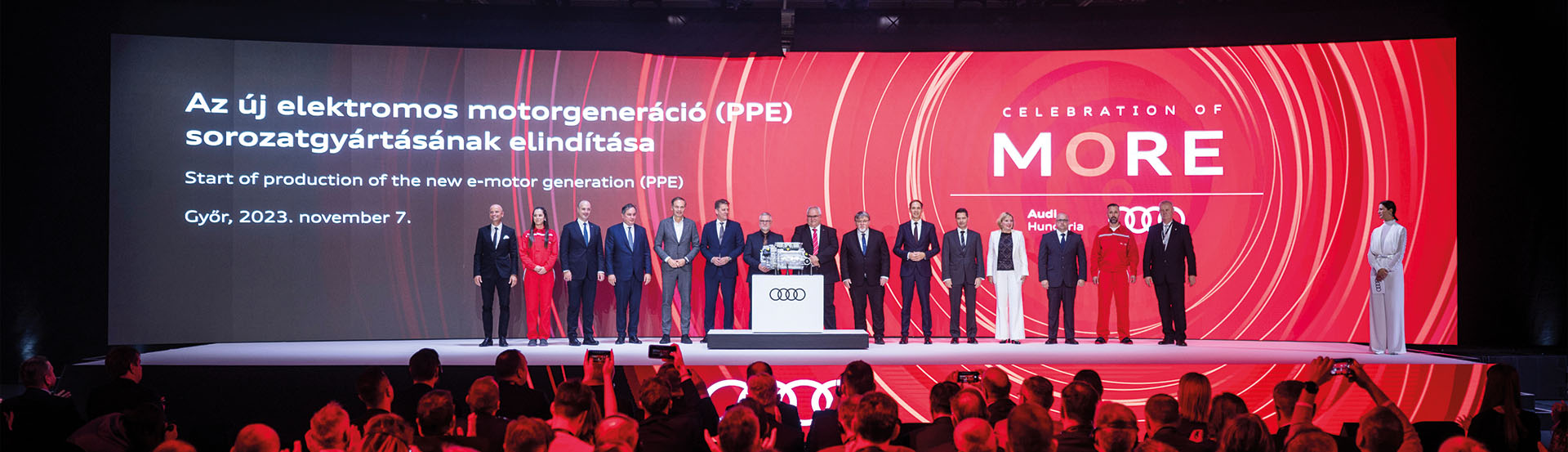
PPE – The dawning of a new era
Let’s now take a look behind the scenes at the inception, closed to outsiders, of a new generation of electric drives, the result of a fantastic collaboration between Technical Development, Pre-Series/Ramp-Up Centre Powertrain (MAC) Production Planning, Production and Quality Assurance.
The story of Audi Hungaria began in 1993 with a small engine factory. Over the past 30 years, the company has grown into the largest powertrain plant and one of the most advanced vehicle manufacturers in the world, with independent technical development facilities, a tool factory producing premium products and a global service portfolio. Today, our community of 12,000 people is ever more successful in its determination to transform the automotive industry. Nothing proves this better than the ceremonial launch of production of our new generation of electric motors in November 2023, a fantastic show where hundreds of invited guests entered the new era of electromobility as our company celebrated its 30th anniversary. However, only true insiders could really understand how exciting the project process, planned to the last detail but often filled with unexpected challenges, that preceded the production of Premium Platform Electric (PPE) drives really was.
The ‘alma mater’ of PPE
Premium Electric Platform – when the PPE project was fully transferred to Audi Hungaria in mid-2022, Korbinian Weber also joined us in Győr from Ingolstadt as Technical Development Project Manager. In 2018, developers started work with production planning on the second generation of Audi’s electric motors.
It was not only the technical hurdles that made this effort such a challenge: the project also involved complex forms of cooperation within the group. The Audi and Porsche brands worked extremely well together, as did AUDI AG’s headquarters in Ingolstadt with Audi Hungaria – with the latter gradually taking over the entire project and assuming increasing responsibility.
“The PPE development process was truly a joint achievement, made possible through our collective enthusiasm and dedication. From the start, developing a completely new product and the many new production technology solutions required a lot of courage and mutual understanding from all the specialist areas. Our reward at the end of the project was a truly innovative and efficient electric motor.”
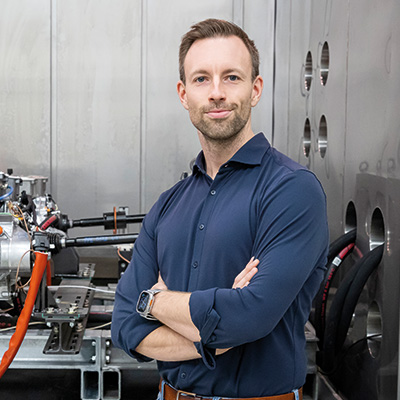

No one in the group is more proud of our outstanding collaboration than I am. The various brands and sites have been working hand in hand for five years, and this collective effort has given us a highly innovative and effective product to offer our clients.
Korbinian Weber
Project Manager, PPE,
Technical Development
Product influence as team success
András Mihályi began his career working on V8 internal combustion engines and, along with many other colleagues, entered the electric world via the e-motor (CBEV) being developed for the Audi e-tron, before joining the PPE project. Many of his colleagues had known each other for a long time, so their personal relationships always enabled them to find the quickest path to solving any problems that arose. And there were plenty of challenges at Pre-Series/Ramp-Up Centre Powertrain (MAC). Using brand-new technical solutions and new production lines, MAC influences design in order to ensure smooth series production, which is a huge task with completely new product types intended for multiple clients. The greatest challenge was posed by an unconventional oil system.
“The engine design and production and testing processes had to be optimised to prevent any possible oil leaks – cost-effectively, and within the given deadlines. The solution to this emerged after a coordination process lasting several months and involving cooperation across various areas, of which I am very proud.”

Influencing design at an early stage is an important task in ensuring the successful launch of series production.
András Mihályi
Analysis Engineer, MAC
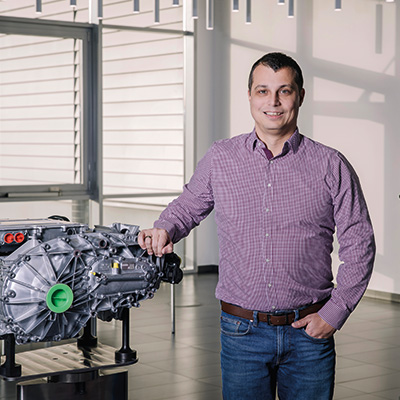
Total transformation
András Hajas has led the PPE production planning team in Ingolstadt since March 2023 and coordinates the 11 Győr-based colleagues responsible for ramping up production lines. Their task is the design and implementation of production technology and production lines, on which Ingolstadt and Győr have worked as a single team from the start.
For the production of PPE drives, the lines were built in an existing hall that previously produced internal combustion engines, with machines that were already in use also being integrated. It was a genuine transformation, and not only in terms of infrastructure, since production planning colleagues were simultaneously switching from working with internal combustion engines to the electric world. One of the special features of the project was having Audi’s Tool Factory commissioned in-house to create the assembly line.
“PPE was also a great test of strength in terms of production depth. In addition to the motor and the stator, certain transmission components are also made here, processes that require new competences and technologies throughout the factory. Tests already show that we have planned stable production lines, but I will only be truly proud and satisfied when the lines are up and running, and we get the required level of quality along with the necessary quantity and cost effectiveness.”
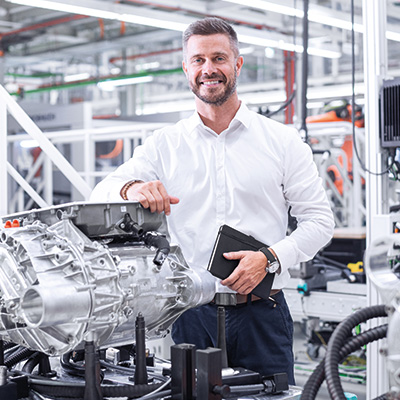

I am particularly proud of being able to participate as a production designer in the birth of Audi’s new family of electric motors in Győr.
Dr András Hajas
Manager, PPE Production Planning,
Ingolstadt
A series of patents
In the case of PPE drives, Audi Hungaria manufactures the complete powertrain, that is, the platform itself. As part of this, Fülöp Viandt is responsible for the stator production line. In addition to the production volume, the biggest innovation is the new technology, even compared to the previous CBEV electric motor. The generational difference is the so-called hairpin, which looks very much like a piece of wire. However, while the CBEV is a wound motor, this double-insulated essentially rudimentary copper component in the PPE aggregate presents the biggest challenge to the production team. This is not a negligible issue, since approximately 157 million pieces will be produced annually. The Audi Hungaria powertrain factory’s path to gripping, clamping and bending it, and then to finding the most optimal subsequent production processes after machining – be they impregnation or polymerisation – required numerous industry patents.
“Relative to the size of the auto industry, the production technology of vehicle drives is developing incredibly rapidly. What we invent today may be obsolete tomorrow. We keep pace with these developments, which also requires other competencies, such as an IT back-end and rapid decision-making.”

Relative to the size of the automotive industry,
the production technology of vehicle drives
is developing incredibly rapidly.
Fülöp Viandt
Manager, PPE, Stator Production
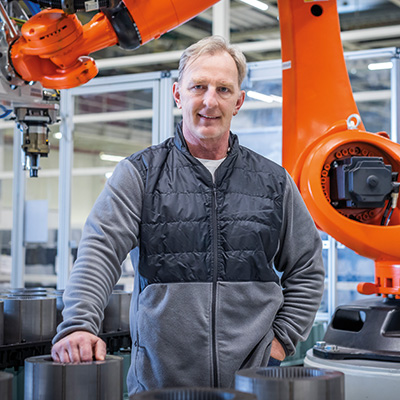
CBEV and PPE – dual responsibility
Thanks to adequate scheduling and planning, the series production quality assurance team started work on PPE processes and components a year before SOP (Start of Production). Zoltán’s team is responsible for purchased parts, which is complemented on this project by quality assurance of production processes, since many assembly steps can later affect the quality of powertrains. Therefore, if any process optimisations or parameter changes are introduced, it is best for this team to also be actively involved. Our colleagues are currently managing both of their existing e-motor projects in parallel, which Zoltán sees as the greatest challenge.
“We have to guarantee the quality assurance of the previous product, the CBEV, for years to come, as well as that of the PPE, of which we plan to produce 2,000 pieces. Our central measuring room and lab for testing materials and electrical components are already in place for internal combustion, so we are able to continuously expand them on a product-specific basis. In our analysis centre equipped for electric drives, we can also carry out tests during motor audits that are only available here, including rotor magnetism measurements.”
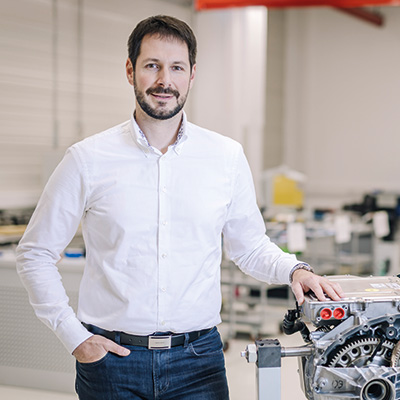

I see it as a great advantage that, by the time our role comes into focus, we will have gathered a lot of experience, as we will know the history of the components.
Zoltán Bozsoki
Component Engineer, Quality Assurance
The pioneer of premium electromobility
The PPE electric platform developed jointly by Audi and Porsche made its debut in cars from both brands, namely the Porsche Macan and the Q6 e-tron from Audi, in time for spring 2024. It is the source of no small amount of pride that the SUV bearing the four-ring logo and made in Ingolstadt is the first model in the company’s history to be propelled by a drive built on the new Premium Platform Electric technology and manufactured entirely in Győr, opening up new dimensions in premium electromobility.
Performance, range, charging, vehicle dynamics and design. The new Q6 e-tron is outstanding in every way that makes a car a joy to drive. In addition to excellent vehicle dynamics and charging performance, its increased efficiency and large range are no less impressive, while the senses are ignited by Audi’s familiar stripped-down aesthetics specially adapted for the e-tron. The interior features technical innovations and novel design solutions that bring new perspectives to electromobility, making it possible to experience technology in motion day after day. Every single Q6 e-tron model driven by the PPE motors made in Győr is a celebration of the multi-faceted expertise, flexibility and openness of the specialist team at Audi Hungaria. New competencies, unprecedented vertical integration in the production of stator and gear components, as well as in the assembly of the drives themselves, cross-discipline collaboration and international project work – the electromobility of the future has arrived.

The new Audi Q6 e-tron is the first model
in the company's history to be propelled by a drive built on the new Premium Platform Electric architecture manufactured entirely in Győr.
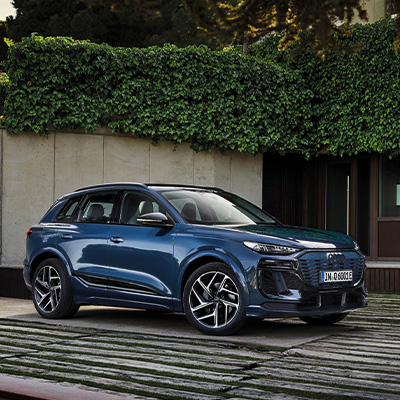
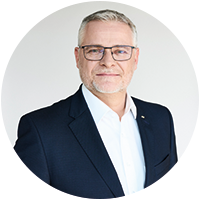
"“Over the past 30 years, our company has developed from a small engine factory producing 1.6 million drives per year into the world’s largest powertrain plant making efficient internal combustion engines and electric drives of premium quality for the entire Volkswagen Group. Powertrain production is also undergoing a dynamic transformation, for which we are constantly preparing our production processes and colleagues. Thanks to the vast experience of my enthusiastic team and our superb motors, we will remain a key bastion of the group in the new era of electromobility.„
Robert Buttenhauser
Member of the Board of Management,
Powertrain Production